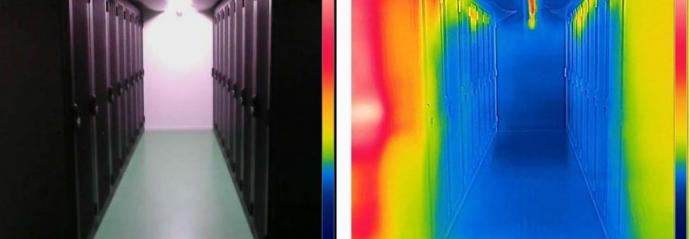
Infrared Thermography
Matter with a temperature above absolute zero emits electromagnetic radiation in solid, liquid and gaseous state, the intensity and wavelength of which depend primarily on temperature. By means of a radiation thermometer the temperature of an object can be measured without contact, taking into account the emission factor of the object, the ambient temperature, the temperature of the measuring sensor and, when measuring long distances, the influence of the atmosphere.
With thermography, a temperature image of an object is built up: the temperature course over the object is shown in different colours or greyscale values. It is based on a single point radiation sensor with a very small opening angle, which is cooled to a low temperature (approximately -200 °C at object temperatures of approximately -100 to 400 °C) to ensure good accuracy. The image is obtained by scanning the object with the help of two high-speed moving mirrors. The measured temperatures are converted into an image, while the information obtained can also be used to perform calculations. For this purpose, digital data storage takes place. Using special software, the data is analysed and presented.
Possible applications of thermography
- Assessment of the building envelope
- Heating and cooling systems
- Industrial plants and processes
Assessment of the building envelope
Building inspection: e.g. at the time of handover, a qualitative assessment of airtightness defects is possible in addition to the inspection of the insulation of facades, floors and roofs. Problem inspections: Infrared thermography is a powerful tool for detecting insulation defects, thermal bridges and air leaks in the event of comfort problems (temperature and draught). Roof leaks can also be detected.
Heating and cooling systems
The non-contact measuring technique allows a quick and therefore efficient control of surface temperatures. This is particularly useful in the case of air-conditioning ceilings, heating elements and underfloor heating during product development, project preparation and on delivery. Of course, troubleshooting of existing systems is also possible.
Installations and processes in the industry
Infrared Thermography makes it possible to measure temperatures which cannot be determined by conventional means, such as a contact thermometer. These include rotating or moving parts (rollers, shafts) and live parts (insulators, busbars, relays, etc.). Large objects or sections can be thermally mapped in a simple manner. Examples are the inspection of (heat) transport lines, boilers, process installations and the like. As thermography can generally be performed on operating installations, it is an ideal means of early detection of possible failures and preventive maintenance. Industrial applications are:
- Monitoring electrical systems: connections, distribution boxes, cabling
- Mechanical systems monitoring: bearings, motors
- Temperature monitoring: casting processes, welding processes, drying processes, rolling mills